Service Agreements for the biopharmaceutical industry
Ensuring equipment availability and product quality
An Alfa Laval Service Agreement is a tailormade service solution, created to meet the needs of your equipment. It ensures you have maximal equipment availability and the highest separation effiency when harvesting your product batches. An Alfa Laval Service Agreement brings high process yield, easy GMP administration and maximum patient safety, while minimizing the risk for out-of-specification batches.
Pharma plant in China saves € 250,000 with Alfa Laval Service Agreement
Due to human error, an Alfa Laval disc stack separator in a plant in northern China producing animal vaccines could not be restarted following a cleaning-in-place procedure. The vaccines are produced using cell cultures and a new batch was ready for harvesting just as the separator stopped working. Due to the delicate nature of the product, the separation had to be completed within 48 hours. Otherwise, the complete batch, worth more than 250,000 Euro, would have to be discarded.
The vaccine producer had a service agreement, which included prioritized emergency support, and contacted Alfa Laval. Even though it was late Sunday night, Alfa Laval immediately dispatched one of its standby service technicians, who arrived at the site a few hours later. The technician solved the problem, and the customer could process the batch in time.
More stories below:
Benefits for biopharma producers
- Operational reliability during harvesting - Regular service ensures high performance and minimizes risks related to product and operator safety.
- Yield - With our performance optimization services you maximize output and secure you get the most out of you starting material.
- Product quality - Preventive maintenance through a service agreement ensures consistent operation from your disk stack separator and predictable product quality.
- GMP administration - We make sure your equipment receives service at the correct intervals, only using genuine spare parts, lubricants, etc., and we deliver all the necessary documentation, eliminating the need for any revalidations.
- Patient safety - With a service agreement you keep your equipment in the exact same condition as it was when it was validated, eliminating the risk of introducing foreign substances in your product.
Downloads
A fully customized service package
You begin by discussing and agreeing with us on the scope of equipment and services that the agreement will cover, and plan when Alfa Laval’s service technicians will perform the preventive maintenance measures and equipment audits. Spare parts are included in the agreement and all procurement is handled by Alfa Laval.
Scope of equipment
Scope of service
Delivery schedule
We handle all practical details
We take full responsibility to maintain the correct service intervals, and we handle all planning and parts procurement. All service interventions are scheduled long in advance and in agreement with you to ensure your production is not disturbed.
The importance of preventive maintenance
Regular, preventive maintenance is key for high performance, reliable uptime, and consistent product quality. If you instead operate until your equipment fails, you run the risk of having to halt production during harvesting. In addition, the separation efficiency will gradually deteriorate over time and cause unnecessary product loss.
Priority support
With an Alfa Laval Service Agreement, you have prioritized support from our team of service engineers 24/7. We offer remote support within a few hours, and we can have personnel at your site within 48 hours.
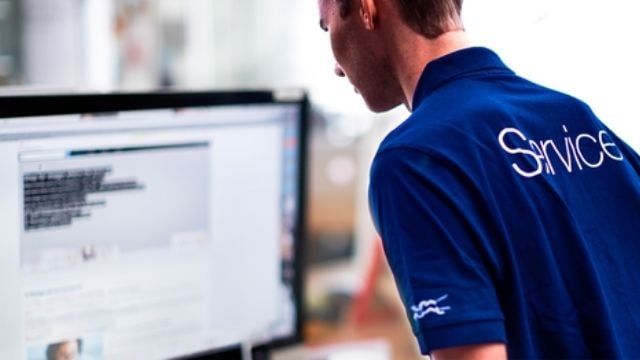
Services
An Alfa Laval Service Agreement can include any service in our 360° Service Portfolio. We recommend:
- Preventive maintenance – Regular inspections and major services are crucial for 100% equipment availability and performance. The services are always carried out by senior technicians with special pharmaceutical training (GMP, GDP, etc.)
- Service patrol – At these regular audits, an Alfa Laval specialist evaluates the status of your separator and makes recommendations on service measures and process adjustments.
- Genuine spare parts – Using original Alfa Laval spare parts is crucial for the operational reliability of your separator and a prerequisite for not having to revalidate your process.
- Technical and GMP documentation – We provide you with all the necessary documentation after each service.
- On-site assistance during operation – An Alfa Laval service technician checks your equipment before each batch is processed and is present during the entire time the separator is in operation.
- Training – We offer a range of training courses for your staff, covering everything you need to know to safely operate and maintain your separator.
- Condition monitoring – Installing a condition monitoring system on your separator allows you to optimize maintenance and increase uptime. The system monitors the separator’s condition and sends immediate alerts if actions are required.
- Remote support – With remote support you have direct access to our service technicians via online video.
Learn more about our complete portfolio of services