2021-05-07 Product News by Ben Green
The hidden costs of plate heat exchangers in the food and beverage industry
Unplanned downtime and product wastage can be incredibly damaging to businesses. Nowhere is this truer than in the fast-paced food and beverage industry, however, it is vital not to neglect the basics.
Ben Green, Food & Water Divisional Manager UK & Ireland at Alfa Laval, explores the consequences of poorly-serviced plate heat exchangers (PHEs) and how preventative maintenance can help safeguard productivity in a time when margins are tighter than ever.
Despite being a precision-engineered piece of equipment, estimates suggest that there are thousands of poorly maintained PHEs out there. When looking to optimise your business operations, it can be easy to overlook this hidden cost that is silently chipping away at your bottom line.
The role of GPHEs in food and beverage
The four main types of PHE are brazed, welded, semi-welded and gasketed. In food and drink processing, the primary compact heat exchanger used is the gasketed plate heat exchanger (GPHE). Here, elastomeric gaskets are fixed to metal plates, creating a seal and separating fluids into different channels. Cool channels lie adjacent to hot channels and fluids flow counter- or co-currently, enabling thermal transfer. This large surface area is why GPHEs are known for their high efficiency.
Problems faced by GPHEs
Fouling
The most common issue encountered is fouling, which is caused by the crystallisation, decomposition or settling of biological matter and particulates. Fouling is much more likely to occur when a GPHE is incorrectly specified or not regularly maintained as flow patterns can become disrupted or blocked.
Fouling is commonplace in the dairy industry, where deposits of whey protein can build up during the pasteurisation process. This build-up is due to the breakdown of proteins present in the milk[1], and although the distribution of the deposits in the PHE can be predicted with a degree of accuracy[2], fouling will occur without proper maintenance.
Whatever the industry, fouling is difficult to remove completely and can lead to unwanted downtime and product spoilage. Therefore, the smartest tactic is to prevent fouling from occurring in the first place.
Other risks
All metal equipment is susceptible to corrosion over time, but in GPHEs, crevice corrosion can appear where each plate is sealed onto the heat exchanger. Additionally, the polymers used to make the gaskets can release chemicals that exacerbate corrosion and lead to gasket failure.
Polymer gaskets can also perish over time for a multitude of reasons: incompatible fluids, UV light exposure, excessive pressure, and more. This can be combatted with preventative maintenance and ensuring the gasket materials are chosen wisely.
Choosing the right gasket material
Gasket material should be customised depending on its specific use. With over 1,700 polymer grades, vulcanising chemicals, and processing materials to consider, choosing the correct material requires a deep technical understanding of how chemicals interact.
Chloroprene rubber, for example, can’t resist very high temperatures while FKMT can, and although EPDMP is very resistant to acids, something else would be more suitable if oils are used in the process. No material suits all processes, so the material choice is critical.
Consequences of running to failure
The problems highlighted above are likely if only reactive maintenance is employed (also known as ‘running to failure’). This is a false economy for businesses trying to save money as these issues bring greater costs in the future.
Equipment failure can cause expensive unplanned downtime, staff may be endangered, product wasted and equipment damaged. Fouling deposits act as insulation, slowing down heat transfer and reducing efficiency and yield greatly over time. Corrosion can release toxic heavy metals into the environment and insurance companies will be reluctant to pay out without evidence of servicing.
Worryingly, a 2015 report even suggested that 1-2.5% of global CO2 emissions can be attributed to PHE fouling[3]. In the wake of the pandemic, when sustainability is being prioritised higher by all industries, Alfa Laval sees ongoing PHE maintenance as an effective way for organisations to hit sustainability goals.
Implementing an effective preventative maintenance strategy
In a time when many businesses are operating within fine margins, allowing equipment to run to failure could prove to be a costly error. It is vital that companies can avoid unplanned downtime and maximise productivity.
Do not let the pervasiveness of GPHEs fool you; expert servicing is required for this highly technical piece of equipment. Preventative maintenance can be treated as a ‘marginal gain’ and is important to staying competitive.
With one of the largest re-gasketing facilities in the UK and over 70 years’ experience, Alfa Laval is perfectly positioned to revitalise GPHEs while minimising the cost to the business.
To download Alfa Laval’s full report ‘Fit for Duty’, visit: www.alfalaval.co.uk/fitforduty
[1] http://www.heatexchanger-fouling.com/papers/papers2015/36_Blanpain-Avet_F.pdf
[2] http://www.heatexchanger-fouling.com/papers/papers2015/35_Khaldi_F.pdf
[3] http://www.heatexchanger-fouling.com/proceedings15.htm
This is Alfa Laval
Alfa Laval is active in the areas of Energy, Marine, and Food & Water, offering its expertise, products, and service to a wide range of industries in some 100 countries. The company is committed to optimizing processes, creating responsible growth, and driving progress – always going the extra mile to support customers in achieving their business goals and sustainability targets.
Alfa Laval’s innovative technologies are dedicated to purifying, refining, and reusing materials, promoting more responsible use of natural resources. They contribute to improved energy efficiency and heat recovery, better water treatment, and reduced emissions. Thereby, Alfa Laval is not only accelerating success for its customers, but also for people and the planet. Making the world better, every day. It’s all about Advancing betterTM.
Alfa Laval has 17,500 employees. Annual sales in 2019 were SEK 46.5 billion (approx. EUR 4.4 billion). The company is listed on Nasdaq OMX.
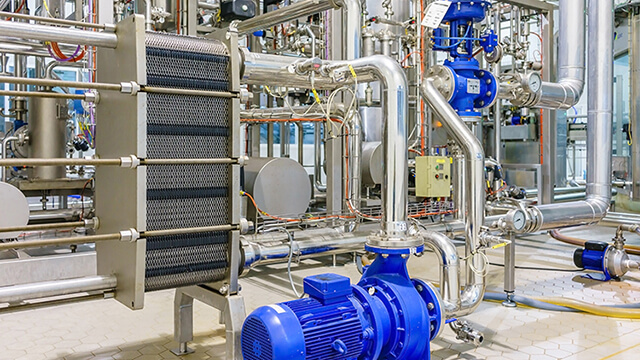